posted
On Thursday, September 23, 2021
in
Blog
Many commercial suppliers use a molding process for manufacturing products, melting and injecting various plastics by a machine into a mold [1-6]. Common plastic materials subjected to extrusion processes are polyethylene (PE), polypropylene, nylon (polyamides) and others. Very often plastic materials contain abrasive components, such as metal fragments or glass-reinforcing fillers, for increasing their durability or achieving other specific properties. Additives like that cause severe abrasive wear of the tools used for forming the plastics. The machines or their components used for carrying out such processes are subjected to many performance challenges caused not only by severe wear but also elevated temperature and corrosion during their operation [1]. The molds are critical components in the injection molding process.
Nitriding is the process best-suited for improving surface properties of injection molding tools, which are typically made of low-alloy steels such as P-20, 4140 or NAK55-type mold steels [6].
There are essentially two major nitriding methods which can be used for hardening of plastic injection molds of larger size: UltraGlow® Ion/Plasma Nitriding and UltraGlow® Gas Nitriding.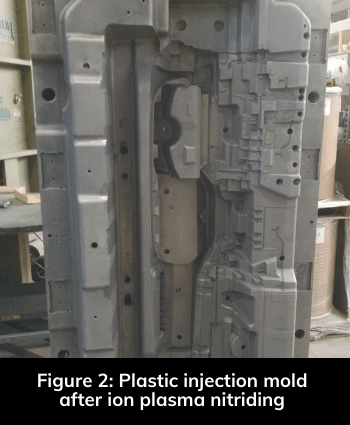
Mechanical Masking for Threaded Holes
In situations where the mold has many areas such as threaded holes, an ion/plasma method should be used since it guarantees ease of mechanical masking for protecting of those threads from becoming brittle. Mechanical masking provides robust fixturing that protects specific areas from being nitrided. The process can be observed and controlled through the port window as seen in Fig. 1.
Little Dimensional Change or Finishing Needed with Nitriding
Nitriding is carried out at 950-1050° F and therefore, there is practically no dimensional changes of the treated product. The treatment also produces a silver/grey hardened surface, which requires very little finishing/polishing, see Fig. 2.
Nitrided surfaces are very hard, see Fig. 3.
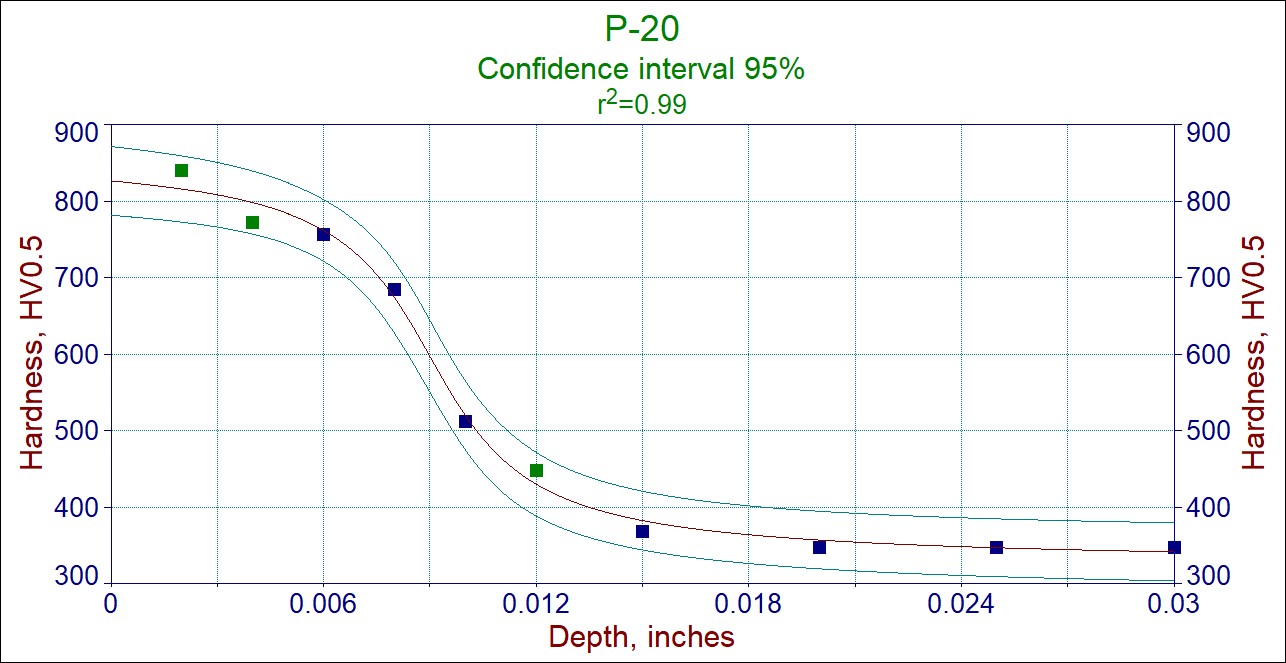
Figure 3 - Hardness profile in nitrided P-20 steel. Please note that 513 HV is an equivalent to 50 HRc and 832 HV is an equivalent to 65 HRc.
Compound Zone
The nitride layer is composed of the compound zone and the diffusion zone, Fig. 4.
Compound zone is built of the Ɛ-Fe2-3N (C) nitrocarbides and ɣ’-Fe4N nitrides, which have very strong anti-corrosion, anti-friction and anti-wear properties enhancing surface durability of the mold. The diffusion layer is rich in a very fine precipitates of chromium and chromium-molybdenum-iron nitrides increasing hardness, providing good support to the compound zone and creating residual compressive stresses near the surface - important for increasing surface fatigue properties of it. It should also be mentioned here that nitrided layers, not carburized layers, have very good thermal stability and maintain their hardness to about 1,100° F.
(RELATED: Read "Wear Resistance of Engineering Components: Carburizing vs. Nitriding.)
Advanced Heat Treat Corp.'s Large Size Capabilities Work Well for Plastic Components / Extruder Screws
Many components of plastic machines, including the extruder screws of very long length can be nitrided by Advanced Heat Treat Corp. [6]. Common steels used for those components are 4140, H-13, Nit135M as well as stainless steels such as 17-4PH, 416 and others are being successfully nitrided at our three locations in Waterloo, Iowa; Monroe, Michigan and Cullman, Alabama.
IOWA AHT ALABAMA AHT MICHIGAN AHT
References
1. “Screws Surfacing Materials for Wear and Corrosion Resistance”, Glycon. Inc. Tecumseh, Michigan, www.glycon.com.
2. E. Rolinski, T. Damirgi, G. Sharp, “Plasma, Gas Nitriding and Nitrocarburizing for Engineering Components and Metal-Forming Tools”, Industrial Heating, May, 2012. 53-56.
3. M. Woods, T. Damirgi, E. Rolinski, “A chrome alternative for corrosive environments”, Hydraulic and Pneumatics, March 12 2015, 3 pages.
4. E. Rolinski, M. Woods, “Engineering the Surface”, Industrial Heating, March, 2019 pp. 28-30.
5. D-C Wen, “Plasma nitriding of plastic mold steel to increase wear- and corrosion properties”, Surface & Coatings Technology 204 (2009), pp. 511-519.
6. E. Rolinski, M. Woods; https://www.ahtcorp.com/articles/blog/enhancing-plastic-extruder-screws-performance-with-ionplasma-and-gas-nitriding/
Who is Doctor Glow?
Dr. Edward Rolinski, aka Doctor Glow, has been studying the plasma/ion nitriding phenomenon since the 1970s and is arguably one of the most knowledgeable people in North America when it comes to nitriding.
The doctor has written countless articles and whitepapers in industry publications and manuals. Some of his most noteworthy contributions include the chapter on "Controlling Plasma Nitriding" in ASTM International (2017) as well as "Nitriding of Titanium Alloys" in the ASM Handbook (2016).
Dr. Edward Rolinski is the Senior Scientist at Advanced Heat Treat Corp. (AHT) and has been employed at AHT since 1994.
LEARN MORE ABOUT DOCTOR GLOW VIEW HIS RECENT ARTICLES
- gas nitriding
- ion nitriding
- nitriding
- plasma nitriding
- plastic