posted
On Monday, May 13, 2019
in
Blog
This article was written by Advanced Heat Treat Corp.'s Rich Johnson, Edward Rolinski and Mikel Woods. It originally appeared on Machine Design's website on October 12, 2018.
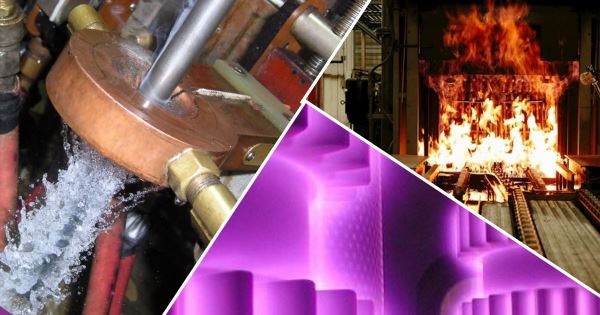
How to Determine the Best Heat Treatment for Your Parts
Long before many of today’s technological advances, people have heat-treated metals to improve their physical and chemical properties for a given application. In the middle ages, blacksmiths forged and tempered metals (albeit in a relatively crude fashion) to create blades, tools, and goods for everyday life. Now, metallurgists and material engineers have a much broader array of specialized techniques and equipment to tailor materials to specific applications. But there are many different heat treatments, such as quenching, tempering, aging, stress relieving, and case hardening. To eliminate confusion, here’s a look at the most common heat treatments, along with their purposes and their pros and cons.
Annealing
Annealing involves elevating a metal’s temperature until it is in an equilibrium state, as defined by its phase diagram. It is used to change the metal’s physical properties such as its hardness, but there can also be local chemical changes, depending on phase transitions. Annealing treatments usually follow machining processing, such as machining and grinding, or even other heat treatments such as quenching.
Quench and Tempering
Quenching involves heating steel above its critical temperature and holding it there long enough to let the microstructure fully change to an austenite phase. The steel is then quenched, a process that rapidly cools the steel by placing it in water, oil, or a polymer solution. This “freezes” its microstructure. What the steel is quenched in to cool controls the cooling rate, and the cooling rate determines the post-quench microstructure. Metallurgists use the metal’s time-temperature-transformation diagram (TTT diagram) to predict the resulting microstructure, whether martensite, bainite, or pearlite. With these structures, ferrous alloys with a carbon composition greater than 0.3wt%. can be extremely hard (>60 HRC), especially the martensite structure. But the increased hardness comes with decreased toughness. Tempering, an annealing process, follows quenching. Steel becomes extremely hard and brittle after quenching, so it undergoes another step to reduce its hardness and increase its ductility, all while maintaining its microstructure.
Tempering a steel below its critical temperature lets it retain its martensitic structure but, if tempered long enough, it gets converted to a mix of ferrite and small carbides, the exact size of which depends on the tempering temperature. This makes the steel softer and more ductile. The key tempering parameters are temperature and time, and they must be precisely controlled to create the desired final hardness. Lower temperatures maintain higher hardness while removing internal stresses, and higher temperatures reduce hardness.
After initial casting or machining, quenching and tempering gives the steel the hardness and strength for making parts with material characteristics. Parts can then be machined to a final state. Quenching and tempering distorts the metal, so parts always go through these two processes before final machining. For parts with additional heat treat processes used to modify surface properties, quench and temper determine a part’s core properties such as hardness, strength, and ductility. (Additional surface hardening treatments will be covered later.)
Stress Relieving
Stress relieving, an annealing step, follows grinding, cold working, welding, or final machining, and is done after the metal has been quenched and tempered to a desired microstructure and strength. This means special consideration must be given to ensure the workpiece is not annealed too closely to its tempering temperatures. This prevents changing the previously achieved hardness and microstructure.
Stress relieving removes internal dislocations or defects, making the metal more dimensionally stable after final processing, such as gas or ion nitriding. Stress relieving is not intended to significantly change the metal’s physical properties; changes to hardness and strength are, in fact, unwanted.
Precipitation Hardening
Precipitation hardening is a special annealing step also known as age hardening due to certain metals hardening over time at sub-critical temperatures. As noted, this method of strengthening metals is limited to those that have undergone quenching and are an over-saturated solution, meaning the material is in a non-equilibrium state with regard to the phases present.
In these alloys, the over-saturated martensite solution is heated (500° to 550°C) and held for 1 to 4 hours, letting precipitates uniformly nucleate and grow. This results in a non-distorted, high tensile and yield strength steel with better wear properties than in its unaged condition. The precipitate phases, composition, and sizes depend on the alloy being aged, but all have the same general effect of strengthening the material.
Not all ferrous alloys are eligible for this hardening mechanism, but martensitic stainless steels such as 17-4, 15-5, and 13-8 are excellent candidates, as well as maraging steels. (The term “maraging” combines the two words "martensitic" and "aging." Those steels have superior strength and toughness without losing malleability, but they cannot hold a good cutting edge. Aging refers to the extended heat-treatment process.) In these alloys, the over-saturated martensite solution is heated (500° to 550°C) and held for 1 to 4 hours, letting precipitates uniformly nucleate and grow. This results in a non-distorted, high tensile and yield strength steel with better wear properties than in its unaged condition.
Induction Hardening
Induction hardening is much like quenching, with one distinct difference: Heating in induction hardening is selective. That’s because in induction hardening, heating is carried done by via magnetic coils designed to match the part’s geometry. This means critical part features can be hardened while the part’s core is not. Instead, the core retains the metal’s strength and ductility. Just as in traditional quenching, it is done using water, oil, or a polymer solution.
Induction hardening can be done on steels with a carbon content greater than 0.3wt%, and to parts with sizes and geometries that can have induction coils designed for them. Induction hardening also significantly reduces processing times needed to harden parts and decreases the risk of decarburization. Unlike traditional heating and quenching, induction is a surface-limited heat treatment with hardened depths ranging from 0.5 to 10 mm.
This was written by Rich Johnson (materials & process manager), Edward Rolinski (sr. scientist), and Mike Woods (president) at Advanced Heat Treat Corp. If you have any questions regarding heat treatments, please feel free to contact them at 319-232-5221.
- annealing
- carbonitriding
- carburizing
- ferritic nitrocarburizing
- gas nitriding
- induction hardening
- ion nitriding
- nitriding
- nitrocarburizing
- plasma nitriding
- precipitation hardening
- quench and temper
- stress relieve
- tempering