posted
On Wednesday, July 28, 2021
in
Blog
E. Roliński, M. Woods
Plasma Nitriding Mechanisms of Low-Density Sintered Metal Products
Download the full PDF here
Abstract
The mechanism of plasma nitriding include the formation of various active species generating nitrogen atoms reacting with the metal. Which species prevail in supplying nitrogen depends on nitriding conditions as well as the nature of the treated metal. Plasma nitriding of low-density powder metal (PM) products results in a formation of the layers whose thicknesses may depend on the gas pressure used for the process. Higher pressure can cause locally deeper penetration of the surface by active nitrogen species formed from ammonia compounds generated by the plasma. While a low processing pressure reduces this effect significantly. The formation mechanism of a locally thicker layer relies on the presence of open porosities in the surface as they can be penetrated by the ammonia species generated by the plasma. The same porosities cannot be penetrated by the ions of nitrogen formed at the same time since their mean free life is much shorter than that of ammonia species.
1. Introduction
Plasma nitriding can be carried out in a typical pressure range of 0.5–5 mbar, depending on the geometrical configuration of the product. When the process is executed at a low pressure, prevailing species are mostly N2 +, N+ ions and active nitrogen atoms in statu nascendi formed in the plasma [1–5]. Those high energy ions as well as fast neutrals collide with the surface causing its sputtering but also adsorption of nitrogen atoms thus leading to the nitriding effect. When the process is carried out at a higher pressure, more active nitrogen atoms in statu nascendi come also from the NHx+-type ions and radicals generated in the plasma. The work of Klümper-Westkamp, Skalecki and others [6, 7] has shown that plasma nitriding can be controlled by measuring the concentration of the ammonia radicals formed by the glow discharge, similarly to affecting ammonia species by controlling nitriding potential in gas nitriding. Increase of gas pressure leads to increase of those ammonia species as demonstrated by [6, 7], see Figure 1.
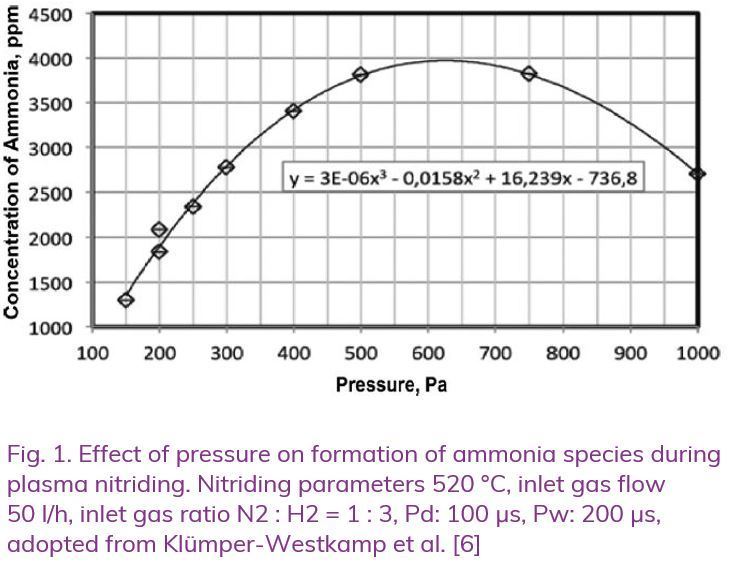
This phenomenon might be especially important when dealing with low-density sintered metal products (PM); the ammonia formed in plasma may cause a gas nitriding-type effect. Generally, low-density PM materials should not be gas nitrided because ammonia may penetrate the entire microstructure of the alloy through interconnected porosities causing its brittleness [8, 9].
The above mentioned spectral differences in plasma composition can result in a typical plasma nitriding effect of the PM and formation of a layer with uniform thickness when pressure is low and a more typical gas nitriding effect and formation of much deeper and non-uniform layer when the pressure is high.
To demonstrate the correctness of the above assumptions, we carried out several different plasma processes as well as a conventional gas process of the typical low-density, 6.8–7.3 g/cm3 PM alloy samples.
2. Experimental procedure
PM samples made from pre-alloyed low-alloy steel FL-4405 (0.4– 0.7 % C, 0.75–0.95 % Mo, 0.05–0.03 % Mn) with a density of 7.1 g/c3 were used for the experiment. The plasma processes were carried out at a temperature of 565 °C in a mixture of N2 : H2 = 3 : 1 with 2 % methane in the pulse plasma system. Before nitriding, all the metal working fluids from forming operation used for the samples were removed by a thermal treatment. A gas nitrocarburizing test was carried out at 570 °C to illustrate the known fact of through-nitriding of low-density PM alloys [9].
3. Results
Figure 2 illustrates that gas nitriding in ammonia of low-density PM material results in a complete saturation of 3–5 mm thick samples with ammonia and their through-nitriding. The internal structure of the sample is also full of cracks and delineations of the grains.
In contrast, plasma nitriding at low-pressure (p = 0.75 mbar) produced a well-visible, continuous structure of a typical compound zone formed the same way as it can be found in a solid, porosity-free steel, see Figure 3. The internal microstructure of the sample is free of the nitrided layer and does not reveal any cracks.
Plasma nitriding test performed at a high pressure (p = 3.5 mbar) produced mixed results, see Figure 4a and b. The compound layer is seen to be much thicker and not uniform. Its thickness is locally very deep. Obviously, ammonia species present in plasma penetrated the open surface porosities much deeper than in the latter experiment. However, the internal structure of the sample is still free of nitrided layer and does not show any visible cracks.
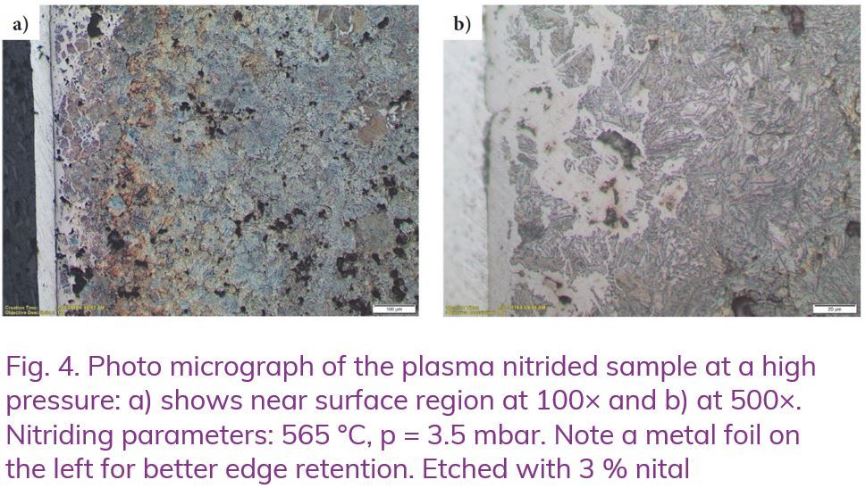
4. Discussion and Conclusions
Low-density powder metal material allows the almost unrestricted penetration of its internal microstructure by ammonia molecules. As a result, through-nitriding of the gas-nitrided sample has been observed, see Figure 2. Side effects of such unwanted ammonia penetration are typically catastrophic to fracture toughness of the component leading to its cracking after the treatment or future brittleness.
The plasma nitriding of identical material may lead to partial penetration of the near surface grains by ammonia molecules and NHx radicals formed from the mixture of nitrogen and hydrogen by processes of ionization, collisions and sputtering at the cathodic surface. It is known that increasing partial pressure of nitrogen to about 50% in the plasma process increases the formation of those ammonia species [6, 7]. A similar effect is also achieved when the total pressure of the gas mixture, and therefore partial pressure of nitrogen, is increased. That is why plasma nitriding at higher pressure results in a locally deeper penetration of the nitrided layer into the surface than at lower gas pressure, see Figure 3 and 4.
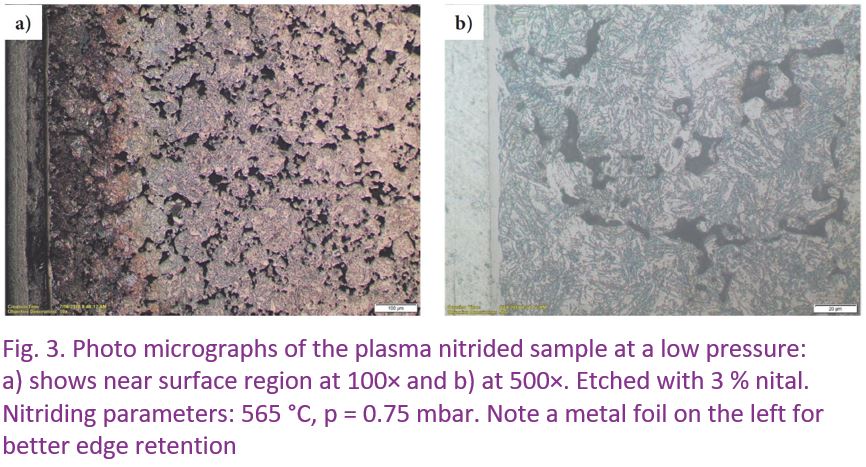
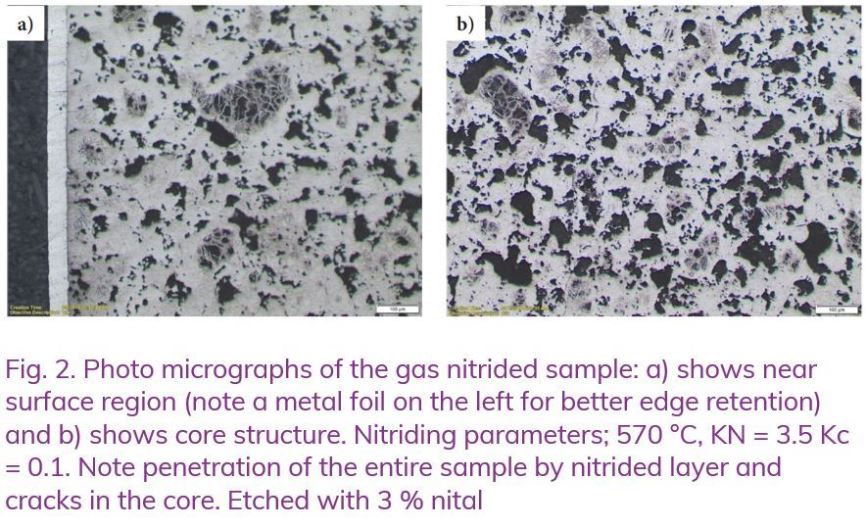
Our observations can be summarized by the graphical model of plasma nitriding when applied to PM material, Figure 5.
When gas nitriding is applied to low-density PM, ammonia species can penetrate it deeply, through a significant thickness of the object, see Figure 5a. Practical results of this phenomena can be observed when a simple experiment is carried out with parts with 10–20 mm thickness. Those parts/samples disintegrate into hundreds of small pieces when impacting a concrete floor.
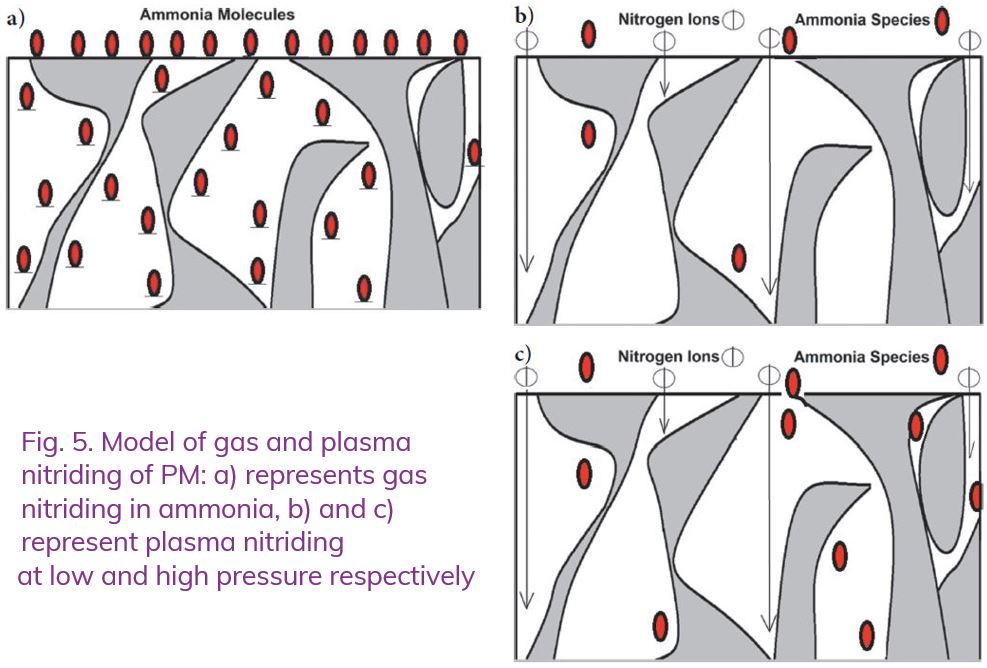
The schematic representation of the nitriding reaction occurring during plasma process is presented in Figure 5b and c. As can be seen, electrically ionized species (ions) move approximately perpendicularly to the surface and are neutralized after first collisions with it. Therefore, they can penetrate only those cavities (porosities) which are open at the surface. On the other hand, ammonia molecules formed in the plasma have much longer intermediate times and free paths (ammonia is detected even at the exhaust of the system in the vacuum pump), and because of that, it can penetrate those porosities much deeper than ions or active nitrogen atoms before being decomposed completely into nitrogen and hydrogen molecules. As a result, since the amount of ammonia generated in plasma depends on the pressure used [6, 7], the layer formed in PM at higher pressure can be much deeper than the layer formed at lower pressure. The severity of this effect might also depend on a local density and homogeneity of PM.
References
1. Roliński, E.: Plasma Assisted Nitriding and Nitrocarburizing of Steel and other Ferrous Alloys. Thermochemical Surface Engineering of Steels, E. J. Mittemeijer, M. A. J. Somers (eds.), Woodhead Publishing, Witney, UK, 2014, pp. 413–449, DOI:10.1016/C2013-0-16318-0
2. Hudis, M.: Study of ion-nitriding. J. Appl. Physics 44 (1973) 4, pp. 1489–1496, DOI:10.1063/1.1662398
3. Walkowicz, J.: Comparative evaluation of the intensity of ion and gas nitriding processes on the basis of conformity analysis of nitrided layers phase composition with the Lehrer’s phase balance diagram. Problemy Eksploatacji 48 (2003) 1, pp. 45–53, in Polish
4. Walkowicz, J.; Supiot, P.; Smolik, J.; Grushin, M.: The influence of the N2-H2 mixture composition on the spectroscopic and temporal behavior of glow discharge characteristics in pulse-supplied nitriding processes. Surf. Coat. Technol. 180–181 (2004), pp. 407–412, DOI:10.1016/j.surfcoat.2003.10.151
5. Danninger, H.; Dlapka, M.: Heat Treatment of Sintered Steels-what is different? HTM J. Heat Treatm. Mat. 73 (2018) 3, pp. 117–130, DOI:10.3139/105.110353
6. Klümper-Westkamp, H.; Gaus, J.-H.; Bischoff, S.; Rohde, J.; Winter, K.-M.: Neueskennzahlbasiertes Regelungskonzept für das kontrollierte Plasmanitrieren und –nitrocarburieren. HTM
7. Skalecki, M.-G.; Klümper-Westkamp, H.; Hoffmann, F.; Zoch, H.-W.; Bischoff, S.; Rohde, J.: Plasma nitriding potential and a new modeling approach for plasma nitriding process control. Proc. 28th ASM Heat Treating Society Conference, 20–22.10.15, Detroit, Michigan, USA, ASM Int., Curran Associates, Red Hook, NY, USA, pp. 325–328
8. Roliński, E.; Sharp, G.; Brondum, K.; Peterson, N.: P/M Turbo Charger and Armature Components: Plasma Nitriding and Nitrocarburizing to Reduce Friction Wear. Proc. SAE World Congress Detroit, Michigan, USA, 11-14.04.05, Paper 2005-01-0722, SAE International, Warrendale, PA, USA
9. Roliński, E.; Konieczny, A.; Sharp, G.: Nature of Surface Changes in Stamping Tools of Gray and Ductile cast Iron During Gas and Plasma Nitrocarburizing. J. Mater. Eng. Perform. 18 (2009) 8, pp. 1052–1059, OI:10.1007/s11665-009-9352-7
Bibliography
DOI:10.1515/htm-2020-0004
HTM J. Heat Treatm. Mat.
76 (2021) 1; page 58-63
© 2021 Walter de Gruyter GmbH, Berlin/Boston, Germany
ISSN 1867-2493, e-ISSN 2194-1831
- edward rolinski
- ion nitriding
- nitriding
- plasma nitriding