posted
On Friday, January 27, 2023
in
Blog
Ion (plasma) nitriding is an environmentally-friendly and safe technology allowing the treatment of ferrous alloys in a very controllable way [1-6]. The active nitrogen species are formed directly at the surface needing hardening and not in the entire vacuum chamber. Therefore, the process uses a very limited amount of processing gases, such as nitrogen and hydrogen, doped occasionally with small amounts of hydrocarbons, if nitrocarburizing is needed. As compared to gas nitriding, this method uses less gas [1]. This is the result of constant ionization and reionization of the processing gases by plasma; while in gas nitriding, the decomposed/cracked ammonia is lost already for the nitriding reaction and must be replaced with fresh gas.
AHT's Large Nitriding Units Are Perfect for Stamping Dies & Gas Compressor Cylinders
Advanced Heat Treat Corp.'s large plasma nitriding equipment allows for the processing of many large parts at the same time. Figures 1-3 show loads of stamping dies and gas compressor cylinders during and after plasma processing.
Stamping dies are the typical cast iron parts treated by plasma nitriding. The main reason for recommending plasma is a good surface roughness after processing especially when the parts are made of the gray cast irons [2-4].
Other cast iron parts quite often treated by plasma are the parts of significant sizes such as gas compressor cylinders. It should be noted here that plasma nitriding allows for easy mechanical masking of the selected surfaces, which should stay soft, such as threaded holes masked off with the bolts as seen in Fig. 2.
Fig. 1. Plasma nitriding of 10 ton+ stamping dies made of cast iron
|
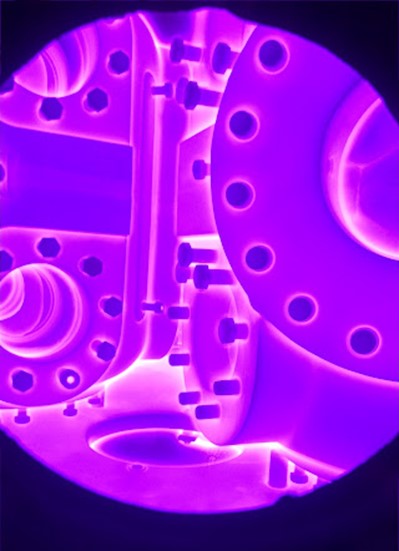
Fig. 2. Plasma nitriding of gas compressor cylinders
|
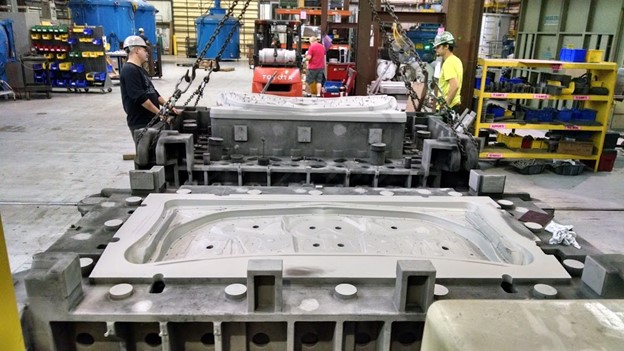
Fig. 3. Stamping dies after plasma nitriding
|
|
Benefits of Plasma Nitriding and Nitrocarburizing of Cast Irons Parts
Plasma nitriding/nitrocarburizing of cast materials, such as gray cast iron, has an advantage over gas nitriding since the active nitrogen species formed from nitrogen and hydrogen during this process do not penetrate deeply into the surface’s open porosities, grooves or other surface imperfections characteristic of gray cast iron. In gas nitriding, ammonia does penetrate those spaces and it also goes into the delineations between graphite particles and the matrix forming locally a much deeper compound layer, resulting in increased volume of the material at the surface. Therefore, roughness of this material is significantly increased after gas nitriding but after plasma nitriding it did not change much. This can be seen in Fig. 4-7 shown below.
When gas nitriding of the gray cast irons would be used, its different nitriding mechanism would result in a deep penetration of the material by the active nitrogen species such NH radicals and this can cause a significant change of the surface roughness [2, 3].
As can be seen in Fig. 4 - 7, plasma nitriding compared to gas nitriding has no nitriding mechanism-limited application characteristics in processing of any cast or porous materials. On the other hand, gas nitriding, because of its ability to penetrate deeply into those materials, cannot be used easily in such applications [2-4].
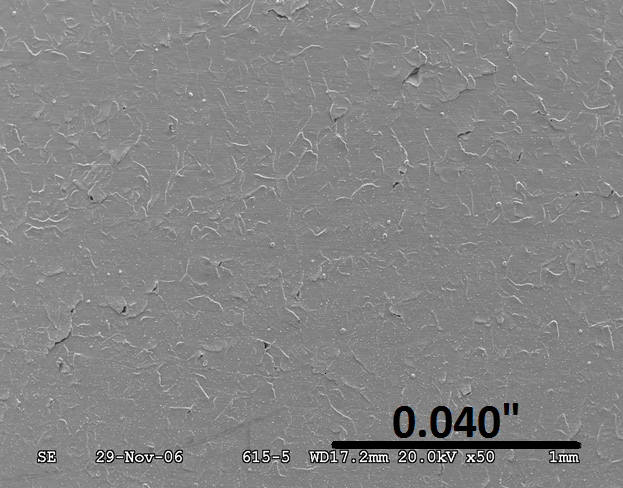
Fig. 4. Surface of gray cast iron after plasma nitrocarburizing at 566° C (1050°F)
|
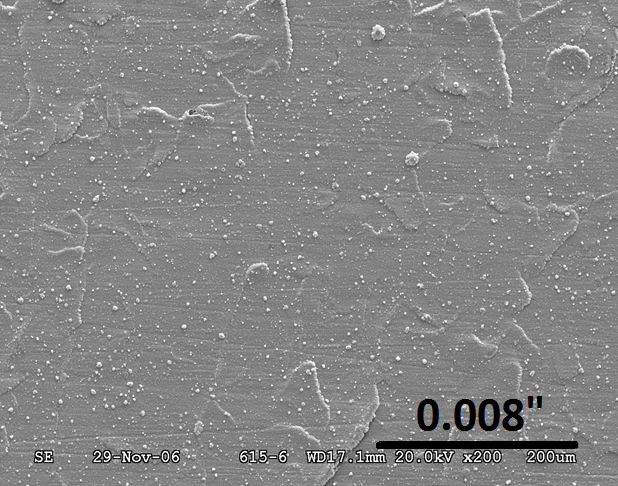
Fig. 5. Surface of gray cast iron after plasma nitrocarburizing at 566° C (1050°F)
|
.png)
Fig. 6. Surface of the gray cast iron after gas nitriding at 566° C (1050°F) at 0.040" magnification
|
.png)
Fig. 7. Surface of the gray cast iron after gas nitriding at 566° C (1050°F) at 0.008" magnification
|
Have Questions about Nitriding or Nitrocarburizing Your Cast Iron Parts? Contact us!
CONTACT US
References
1) E. Rolinski,” Plasma Assisted Nitriding and Nitrocarburizing of Steel and other Ferrous Alloys”, Chapter 11 in Thermochemical Surface Engineering of Steels, Ed. E. J. Mittemeijer and M. A. J. Somers, Pub. Woodhead Publishing, 2014, pp 413-449.
2) E. Rolinski, A. Konieczny, G. Sharp, “Nature of Surface Changes in Stamping Tools of Gray and Ductile cast Iron During Gas and Plasma Nitrocarburizing”, Journal of Materials Engineering and Performance, 2009, Vol. 18 No 8, pp 1052-1059.
3) E. Rolinski, A. Konieczny, G. Sharp, “Influence of Nitriding Mechanisms on Surface Roughness of Plasma and Gas Nitrided/Nitrocarburized Gray Cast Iron”, Heat Treating Progress, March/April 2007, pp 39-46.
4) E. Rolinski, G. Sharp and A. Konieczny, “Plasma Nitriding Automotive Stamping Dies”, Heat Treating Progress, September/October 2006, Vol. 6, No 5, pp 19-23.
5) E. Rolinski, “Surface Roughness: Effect of Nitriding”, in Encyclopedia of Iron, Steel, and Their Alloys”. DOI: 10.1081/E-EISA-120050825, 2015, Ed. By Taylor & Francis. pp 3534-3550.
6) E. Rolinski, M. Woods, T. Damirgi, and G. Sharp, “Improving Performance of Stamping Dies with Ion/Plasma Nitriding” and “Ion Nitriding for Surface Hardening of Aerospace Components”, Industrial Heating, November, 2015, pp. 40-46.
- cast iron
- ion nitriding
- nitriding
- nitrocarburizing
- plasma nitriding
- stamping dies