posted
On Friday, April 1, 2022
in
Blog
Introduction
Titanium and its alloys with aluminum, vanadium, nickel, ruthenium, molybdenum, chromium or zirconium have many unique properties. The alloying is used for the purpose of improving various mechanical properties, heat resistance, conductivity, microstructure, creep, ductility, and corrosion resistance of many engineering components [1, 2]. Special chemical properties of titanium are related to its very high corrosion resistance in oxidizing environments and that depends on formation of the tightly adherent, protective oxide film TiO2. This oxide is resistant to many chemical environments, specifically seawater and other chloride-brine media [1, 15]. Titanium has a low thermal and electrical conductivities but it is slightly paramagnetic.
Despite of all of the attractive properties listed above, titanium has very poor tribological performance and has to be surface treated in many applications [1-16]. Therefore, for many years intensive work has been carried out on oxidizing and other gas treatments [1, 2 and 24]. At the moment, nitriding is the most common and rational diffusion treatment which can be used for all-over surface hardening of titanium products [3-23]. Nitrided titanium has a gold/yellow color of the TiN nitride enhancing attractiveness of the treatment in many applications, Fig. 1.
Plasma nitriding is carried out in a vacuum-type vessel where the treated part has the cathodic polarization and the vessel wall is the anode. Ions of nitrogen and neutrals accelerated in the Crookes Dark Space achieve high energy and bombard the cathode surface activating it and causing chemisorption of nitrogen atoms in statu nascendi and their diffusion. The process can be monitored and controlled optically through the special window, see Fig. 2.
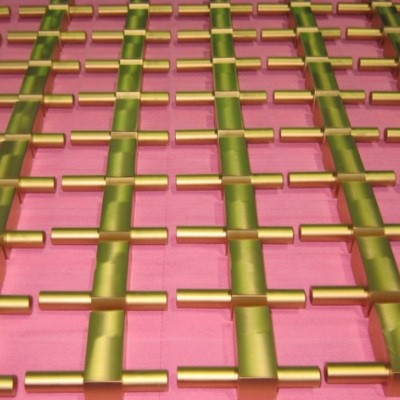
Figure 1
Titanium parts after plasma/ion nitriding at Midport facility of Advanced Heat Treat Corp. in Waterloo, Iowa.
|
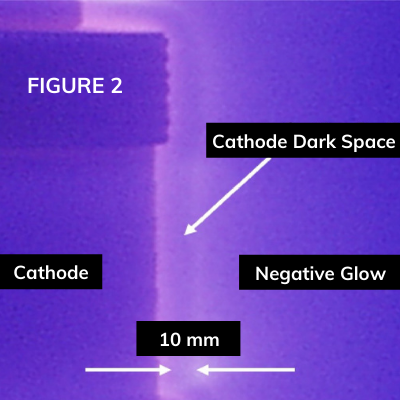
Figure 2
The near cathode glow discharge zones during processing complex geometry part. Picture adopted from [5].
|
Nitriding
The nitriding treatment is typically carried out at temperature >600° C depending on the alloy although some of the medical applications may require lower temperature. Titanium has a great chemical affinity not only for nitrogen but also for oxygen and carbon, Fig. 2 [5]. Therefore, vacuum vessel used for plasma nitriding has to have a good quality and nitrogen has to be very pure to minimize effect of those impurities.
Figure 3
Effect of temperature on standard enthalpy of formation of titanium compounds with, nitrogen, carbon, oxygen and hydrogen. Graph adopted from H. Göhring, [5].
The graph in Fig. 4 shows that the formation of δ-TiN nitride occurs at a very low partial pressure of nitrogen or at a very low nitriding potential. Both values are so low that it seems impossible to exert a practical control of the atmosphere in order to avoid the formation of TiN [5]. The presence of hydrogen in the nitriding atmosphere has positive effects on lowering the oxidizing potential of the atmosphere [7]. Hydrogen added to the atmosphere enhances the nitrogen adsorption and also diffusion depth and nitrogen concentration. Also, nitriding with hydrogen-containing gases modifies the microstructure of the nitrided layer. As a result, the layer produced in ammonia is thicker and has greater hardness compared to the layer produced by plasma nitriding in a mixture of nitrogen with hydrogen or with nitrogen and argon.
Figure 4
Equilibrium nitrogen, partial pressure and nitriding potential necessary for δ-TiN formation. Graph adapted from [5, 6].
Figure 5
Hardness profiles of gas and ion nitrided specimens of Ti6Al4V alloy: nitriding temperature=800° C, and time=24 hr. Graph adopted from Spies [7, 8].
However, it has to be remembered that during gas nitriding in ammonia, the partial pressure of hydrogen is very high, well above 700 mbar and it is much higher than it is in plasma or vacuum nitriding. Therefore, the effect of hydrogen is greater in enhancing surface reaction and it results in a thicker compound layer as well as deeper diffusion depth and higher concentration of nitrogen. The negative side of such an approach is the absorption of hydrogen by the alloy and a need for the dehydration treatment after that. It should also be noted that at the temperatures used in nitriding of titanium alloys, ammonia is almost fully decomposed and the process is in fact carried out in a mixture of 75% hydrogen and 25% nitrogen [5]. Vacuum nitriding uses nitrogen pressure in the range of 0.5-840 mbar after achieving a “hard” vacuum [5].
Phases formed during nitriding of titanium are: TiN, Ti2N and ɑTi, see phase diagram in Fig. 6 and photo micrograph in Fig. 7.
Figure 6
Ti-N Binary Phase Diagram per Khidirov Okamoto in [5].
|
..png)
Figure 7
Photomicrograph of the surface layer produced on titanium by plasma nitriding at 1030° C. Photomicrograph adopted from E. Rolinski [5].
|
Commercial gas nitriding of titanium alloys was researched at MIT and introduced in the 1950's. It was a classical way for improving surface hardness and wear resistance [5]. This method is effective but as mentioned before, introduces hydrogen from ammonia into titanium, which unfortunately forms brittle hydrides and therefore the process is in fact the nitride-hydriding [5, 7, and 8].
Plasma/ion nitriding of titanium has been researched for the last 50 years and it is a very effective way of surface hardening of many engineering components made of this metal and its alloys [5-16]. TiN layer, which always forms at the surface during this process, has the hardness in the range 1800-2100 HV and its golden color is very attractive in many applications. Underneath Ti2N layer is less hard, about 1000HV but few times thicker than TiN. Their ratio depends on nitriding temperature, the higher it is, the more TiN forms [5]. For example, relative zone thickness is:
- at nitriding temperature 700 C° TiN: Ti2N: αTi=1.0:8.1:105.0 and
- at nitriding temperature 1000 C° TiN: Ti2N: αTi=1.0:3.5:25.8.
Solubility of nitrogen in titanium is very high so the diffusion zone formed below both compound zones can reach high hardness in the range of 800-900 HV maximum and with the total thickness 20-50 µm. In titanium alloys structural situation is more complicated and also formation other alloyed nitrides have been reported [9, 10].
Typical structure of nitrided titanium alloy is shown in Fig. 8.
Figure 8
Ion Nitrided Ti6Al4V Sample: TN=765° C, 28 h, nitrogen adopted from [5].
|
Figure 9
Concentration depth profiles (GDOS) of ion nitrided Ti6Al4V sample: TN=765° C, 28 h, nitrogen per E. Rolinski, adopted from [5].
|
As can be seen in Fig. 9, nitrided layer very often has impurities of carbon and oxygen in it. Therefore, as mentioned before, quality of the vacuum in ion nitriding vessel used for processing titanium alloys has to be very good for avoiding unnecessary “doping” of the layer with C and O atoms. Nitrided layer formed in titanium alloys is much more complex than the layer formed in pure titanium. Also, presence of hydrogen in nitriding atmosphere or gas nitriding in ammonia leads to formation of titanium hydrides. All of the above is illustrated in Fig. 10.
Figure 10
Model of structure of gas and plasma nitrided cases of (ɑ+β) alloy Ti6Al-4V after nitriding in upper (ɑ+β) region. Adopted from H. J. Spies [8, 9].
Benefits of Nitriding Properties of Nitrided Titanium Alloys
Depending on nitriding temperature, nitrided layer formed in titanium or its alloys has more or less fraction of TiN nitride versus Ti2N nitride and α(Ti)-solid solution zone. A typical microhardness profile formed in the Ti6Al4 sample is shown in Fig. 11. It should be noted that hardness of the near surface zone and nitrides could not be measured with a regular microhardness tester and it is very likely much higher as reported in the literature [5].
Wear resistance of nitrided titanium alloys is much better than in the non-nitrided condition even at comparatively high contact-Hertzian stress of 400 MPa, see Fig. 12. Roughening of the surface after nitriding at high temperature has obviously negative effect on wear by friction as it is demonstrated by the curve for 1030° C.
Figure 11
Knoop microhardness of Ti6Al4V alloy part plasma nitrided in the Midport facility of Advanced Heat Treat Corp. in Waterloo, Iowa.
|
Figure 12
Linear wear of WT3-1 (Ti6Al2.5Mo2Cr) samples ion nitrided at various temperatures as a function of friction time at a constant surface pressure of 400 MPa, adopted from E. Rolinski [5, 13].
|
Designing engineers are very often asked which nitrided alloy would perform better in tribological applications. The answer is shown in Fig. 13. Both stainless steels; the martensitic and the austenitic after nitriding don't match performance of the titanium alloy.
Figure 13
Linear wear of WT3-1, nitrided at 830° C, as well as of 1H18N9T (austenitic) and H17N2 (martensitic) stainless steels, plasma nitrided at 585° C, as a function of time at constant unit pressure of 400 MPa, adopted from E. Rolinski [5].
Nitriding increases corrosion resistance of titanium and its alloy in many corrosive environments and nitriding temperature has a small effect on it [5].
Figure 14
Potentiodynamic curves of anodic polarization in 15% H2SO4 of titanium alloy-WT3-1 in a non nitrided condition and after nitriding at various temperatures, SCE, saturated calomel electrode, adopted from E. Rolinski [6].
In comparison to nitrided steels, corrosion resistance of nitrided titanium is much higher, Fig. 15.
Bending fatigue properties of titanium alloys after nitriding have been researched very aggressively in the last 30 years [5]. It appears that in regards to pure titanium only the low temperature treatment increases bending strength, see Fig. 16. This is very likely related to the fact that very hard and brittle zone of TiN nitride becomes too thick at a high nitriding temperature and increases brittleness of the nitrided layer casing premature failure of the sample. Also change of the grain size in titanium during annealing of the structure at nitriding temperature may play a role [5].
Figure 15
Potentiodynamic curves of anodic polarization in 0.05 M Na2SO4+0.1 M NaCl solution of pH 3.0 for WT3-1 nitrided at 830° C, and for 1H18N9T (austenitic) and H17N2 (martensitic) stainless steels, plasma nitrided at 585° C, adopted from E. Rolinski [6].
Figure 16
Fatigue strength of titanium after various nitriding treatments adopted from Morita [21].
Similarly, negative results reported by other scientists indicate that the fatigue strength of titanium alloys is lower after nitriding unless, the TiN zone is removed from the layer. Also, comparatively low aging temperatures of those alloys versus nitriding temperatures, have negative effect on bending fatigue properties of them [5].
Examples of Plasma Nitrided Titanium Parts
Nitriding of titanium can be successful in plasma/ion-nitriding. A couple things to consider is the prior heat treatment of the material. Processing of titanium is done at 660° to 800°C. To ensure there is not dimensional changes to the part processing must be complete 28°C below any prior heat treatment. Temperature control is critical for success. Another consideration is that no masking can be done during this process. All surfaces will be treated during the processing.
Part in Electric Car
|
Firearm Component
|
Part for Stamping Application
|
Advanced Heat Treat Corp. has a very broad range of ion and gas nitriding equipment, used for treating ferrous and titanium alloys. We can run miniature-type parts as well as 10 meters shafts with a very high accuracy.
Questions About Nitriding Titanium Alloys?
CONTACT US.
References
1) S. Lampman, Wrought Titanium and Titanium Alloys, 1990, Metals Handbook Vol 2, Properties and Selection: Nonferrous Alloys and Special-Purpose Materials, Ed ASM International, pp 592-633.
2) F.H Froes, editor, “TITANIUM Physical Metallurgy Processing and Applications”, ASM International, 2015, ISBN-13: 978-1-62708-079-8, 404 pages.
3) E. Rolinski, B. Cowell, “Plasma Nitride Surface Hardening of Titanium for Aerospace and Armament Applications”, Aerospace & Defense Technology, April 2012, pp. 10-12.
4) H. Okamoto, N-T (Nitrogen-Titanium), JPEDAV, DOI: 10.1007/s11669-012-0153-6, 1547-7037 ©ASM International.
5) E. Rolinski, “Nitriding of Titanium Alloys”, ASM Handbook, ASM International Vol. 4E, Heat Treating of Nonferrous Alloys, Volume Editor, G. E. Totten, 2016, pp.604-621.
6) E. Rolinski, “Surface properties of plasma nitrided titanium alloys”, Mater. Sci. Eng., Vol. 108, 1989, p 37-44.
7) M. Jung, F. Hoffmann and P. Mayr, Drucknitrieren von Titanbasiswerkstoffen, HTM, 53, 1998, 5, pp 283-293.
8) H.-J. Spies, B. Reinhold, and K. Wilsdorf, Gas Nitriding-Process Control and Nitriding Non-Ferrous Alloys, Surface Engineering, Vol. 17, 2001, No 1, p 41-54.
9) H.-J. Spies, Randschichtbehandlung von Aluminum- und Titanlegierungen –ein Überblic. (Surface Engineering of Aluminum and Titanium alloys: An Overview), HTM J. Heat Treatm. Mat. 65, 2010, 2, pp. 63-74, in German.
10) Krzysztof Szymkiewicz, Jerzy Morgiel, Łukasz Maj, Małgorzata Pomorska, Michał Tarnowski, Tadeusz Wierzchoń, “TEM investigations of active screen plasma nitrided Ti6Al4V and Ti6Al7Nb alloys”, Surface & Coatings Technology, 383(2020), 1-8.
11) E. Rolinski, T. Damirgi and M. Woods, “Ion nitriding of Ferrous and Titanium Alloys for Gear Application”, Thermal Processing for Gear Solutions, Fall/Winter 2015, pp. 36-40.
12) E. Rolinski, G. Sharp, D.F. Cowgill and D.J. Peterman, “Ion nitriding of titanium alpha beta alloys for fusion reactor applications”, Journal of Nuclear Materials 252(1998), pp 200-208.
13) E. Rolinski, “Surface properties of plasma nitrided titanium alloys”, Materials Science and Engineering, 108(1989) 77-44.
14) E. Rolinski, “Effect of nitriding on the surface structure of titanium”, Journal of the Less-Common Metals, 141 (1988) L.1 I-L.14.
15) E. Rolinski, “Mechanism of high-temperature plasma nitriding of titanium”, Materials Science and Engineering, 100 (1988) 193-199.
16) E. Rolinski, “Plasma nitriding of titanium alloys”, Proc. Conference:” Techniques for Surface Treatment of Metals”, Rzeszow, (1988) 77-84 in Polish.
17) E. Rolinski, L. Walis and A. Ciurapinski, “Metallographic and radio isotopic investigation of the plasma nitrided Ti6Al2.5Mo2Cr alloy with alpha plus beta structure”, Journal of the Less-Common Metals, 136(1987) 135-145.
18) T. Karpinski, E. Rolinski, K.T. Rie, Th. Lampe and St. Eisenberg, “Mikrogefuge und Wachmskinetik von Plasmanitrierschichten”, Technischer Fortschritt. DGM, Stuttgart, May 1985, 107 in German.
19) J. Mańkowski, E. Roliński and J. Flis, Effect of Plasma Nitriding on Corrosion Behavior of Stainless Steels in Sulphate and Chloride Solutions, Proc. 1st Int. Conf on Surface Engineering, London, 1986, May 14-16, Metals Institute, London, 1986. p 21.
20) T. Morita, H. Takashi, M. Shimizu and K. Kawasaki, Factors Controlling the Fatigue Strength of Nitrided Titanium, Fatigue & Fracture of Engineering Materials and Structures, Vol. 20, No. 1, 1997, p 85-92.
21) E. Rolinski “Plasma Nitriding of Titanium and Its Alloys”. /Dissertation/, Ed. By Politechnika Warszawska, 1988,121 pages, in Polish.
22) K. –T. Rie, Th. Lampe and St. Eisenberg, Plasma Heat Treatment of Titanium Alloy Ti-6Al-4V: Effect of Gas Composition and Temperature, Surface Engineering, 1985, 1, No 3, pp 198-202.
23) T. L. Christiansen, M.S. Jellesen, M. A.J. Somers, “Future trends in gaseous surface hardening of titanium and titanium alloys”, La Metallurgia Italiana - n. 9 2018, 13, pp. 13-22.
- edward rolinski
- ion nitriding
- titanium