posted
On Wednesday, June 23, 2021
in
Blog
Originally appeared in Heat Treating Progress' March/April 2007 issue. Click Here to see the original content.
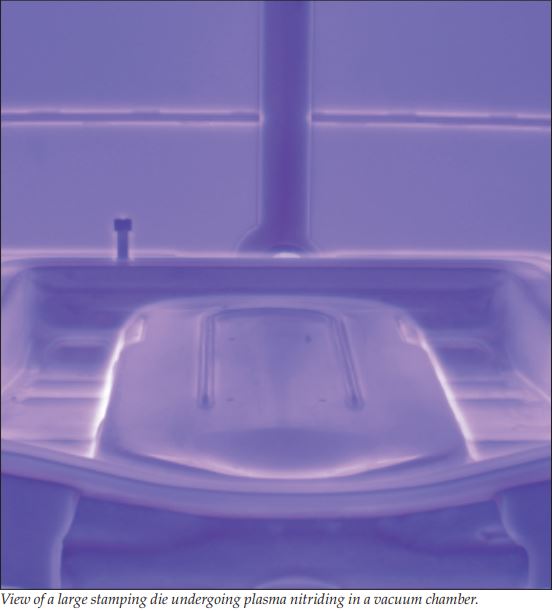
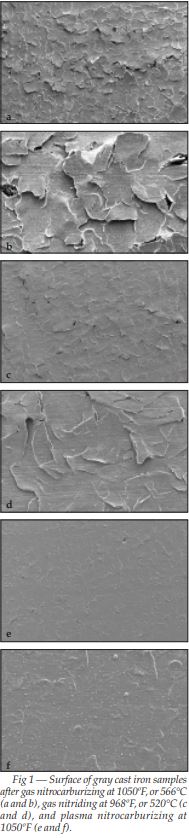
The mechanism of plasma (ion) nitriding has been studied extensively during the past 40 years. There is general agreement that nitrogen ions and radicals such as N+, N2+, NH+, NH2+, as well as fast neutral nitrogen molecules play a significant role in nitrogen transfer. This occurs either by generating active nitrogen atoms on the cathodic part surface, or by attaching to iron atoms sputtered from the surface and redeposited back on the cathode in the form of nitrides.
The gas-nitriding mechanism using ammonia is less controversial and has been considered as a catalytic reaction of ammonia with iron which leads to the formation of the active nitrogen atoms in statu nascendi and their chemisorption according to the reaction:
2NH3→2Nad+3H2
The differences in nitrogen-transfer mechanisms between the two methods have various practical consequences. For example, plasma nitriding is considered as a low nitriding-potential method, unable to produce a thick compound zone, and plasma nitriding does not penetrate small holes, cavities, etc. and therefore the process can be used for hardening sintered low-density iron parts. This characteristic of plasma is also used to advantage in mechanical masking. By comparison, gas nitriding can produce a compound zone (white layer) of practically any thickness by controlling the nitriding potential using hydrogen or oxygen sensors and modern automatic methods. Also, gas nitriding can be used for hardening parts having small holes, such as those in diesel injector plungers, and nitriding the entire surface of any product. Proper identification of the respective advantages and disadvantages of the two methods could significantly improve their use.
The differences in plasma and gas nitriding are demonstrated on common gray cast irons, which are frequently used for tooling in many stamping operations. This inexpensive material offers a good combination of cast mechanical properties and damping, which are very important in large, 20-30,000-lb (9-13,600 kg) tooling.
High-quality finishing of such tools to Class A-surface requirements after thermochemical treatment is of paramount importance to achieve good, long lasting performance in manufacturing applications. Surface quality requirements are even more critical for tools designated for stamping modern materials such as advanced high strength steels (AHSS), including DP490 dual-phase steel. Therefore, post-nitriding roughness must be kept to a minimum and any finishing operations should not be too costly. The authors observed that gray cast iron dies become rougher after gas nitriding and require more finishing than the plasma-nitrided dies, which has a high possibility of being a result differences in the nitriding mechanisms of the two methods.
Experimental
All experiments were performed on G3500 gray cast iron samples having the following chemical composition in wt%:
2.8-3.2C, 1.5-2.2 Si, 0.7-1.0 Mn, 0.35-0.50 Cr, 0.35-0.50 Mo, <0.7 Cu, <0.15 S,
<0.15 P, bal. Fe
Samples were ground using metallographic polishing papers, finishing with 600x
grit. Plasma nitrocarburizing was performed in a nitrogen and hydrogen gas mixture containing 2% methane. Controllable gas nitriding was performed in an ammonia, nitrogen, and hydrogen gas mixture, and also with carbon dioxide in the case of the nitrocarburizing cycle. The gas nitriding system was equipped with a hydrogen sensor and automatic control of the nitriding potential. Process parameters are shown in Table 1.
Results
High-temperature (1050°F or 566°C) gas nitrocarburizing caused a significantly rougher surface. Steps taken to minimize the problem included trying nitriding instead of nitrocarburizing and using a lower processing temperature (968°F or 520°C) and lower nitriding potential. These processing conditions reduced surface roughness compared with the nitrocarburized samples, but surface roughness was still unsatisfactory. By comparison, plasma processing resulted in a significantly lower surface roughness with very few open microgrooves and cavities in the surface (Figs. 1 and 2). Data on surface roughness after processing are shown in Table 2. Rmax for the plasma-nitrided surfaces, although much lower than after gas nitriding, are still comparatively high for stamping tool applications. However, it should be noted that these picks are made of loose deposit of the nitrides from plasma, which do not adhere too strongly to the surface and can be easily removed by a simple polishing operation with a soft-wire brush.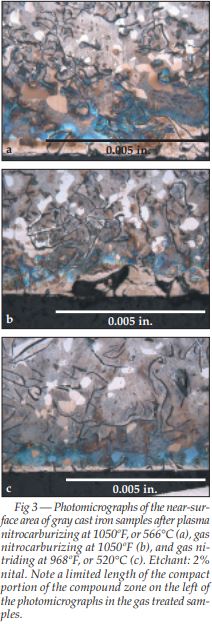
Compound zones formed in the gas nitrocarburized and nitrided samples had a very uneven thickness with an inconsistent compact portion and tree-like roots along the flakes of graphite and between surface cracks and imperfections (Fig. 3). Total penetration of the internal structure by these roots of the compound zone exceeded several times the thickness of the compact portion of the zone. Therefore, the specific volume of the near-surface layer became locally larger than that of the base matrix, which resulted in the areas of increased volume to extend above the original surface. Furthermore, the cracking and plastic deformation in this region added to the roughening effect.
In the as-plasma-treated sample, the compound zone was very uniform and compact without any significant defects.
Industrial Case Studies
In the Industrial applications, the negative effects of gas nitriding of gray cast iron stamping and forming dies may even be more visible than in the laboratory because these types of the large castings very often have microstructural defects, lack of homogeneity, surface decarburization, and kish graphite flakes shown in Figs. 4 and 5. It is possible that the "openings" near graphite flakes in the surface of gray cast iron, such as those in Fig. 5, allow ammonia to penetrate deeper into material.
Discussion
Surface defects of gray cast iron are created during the machining operations performed on the as-cast surface in the process of the final shaping of the die geometry result from the physical differences between graphite and the mostly pearlitic matirx. Graphite flakes allow easy free machining of cast iron by introducing discontinuities in the metal matrix. Therefore, during machining, chips are broken rather than plastically deformed or smeared over the surface by the cutting tool. As a result of the clear-cut machining, surface voids and cracks are not filled with the metallic components of the matrix, but rather with graphite, or they stay open. Also, the interface between graphite flakes and the matrix nay not be as coherent near the surface as in the core.
During plasm nitriding materials having a porous surface, such as cast iron, the hardened layers produced are superior to layers produced by gas nitriding. Plasma-produced layers are very compact, which promotes a much smoother surface, This is the result of the inability of the active species generated in plasma above the cathode to penetrate small cavities and crevices present below the surface of the material being processed. These species are very likely N2+ ions, also considered as precursors for forming any other ions in plasma nitriding.
Very complex reactions between those ions result in the formation of active nitrogen (N) atoms, which have a lifetime greater than 1.0 second, and are primary species responsible for plasma nitriding. Although the mean free path of the N atoms along a straight line might be comparatively long depending on the pressure used, their collisions with the solid workpiece deactivate them bef
ore they can enter the confined spaces below the cathode surface and, therefore, their range is very limited. Additionally, products of the reactive sputtering partially come back to the cathode surface and fill the cavities and micropores, minimizing penetration of the nitriding species by simple mechanical masking.
In contrast to plasma nitriding, ammonia molecules in gas nitriding enter all of the confined spaces at first and then generate active nitrogen atoms during collisions with the solid (walls of the cavities). Therefore, they have a longer lasting effect, and by penetrating deeply, produce very significant roots of the compound zone below the surface (Fig. 6). Those processes increase specific volume of the near-surface layer, and by causing local plastic deformation of the material, lead to local bulging of the surface, thus increasing its roughness.
Conclusion
Based on the evaluation of experimental data, simple, logical consequences of the differences between plasma- and gas-nitriding mechanisms demonstrate that there are limitations to what degree results of these two methods are identical. In processing products made of gray cast irons, plasma nitriding does not penetrate deep into the material and, therefore, formation of the nitrided layer is limited to only the surface of the product. Therefore, plasma nitriding has no nitriding mechanism-limited application characteristics in processing of any cast or porous materials. On the other hand, gas nitriding, because of its ability to penetrate deeply into those materials, cannot be used easily in such applications.
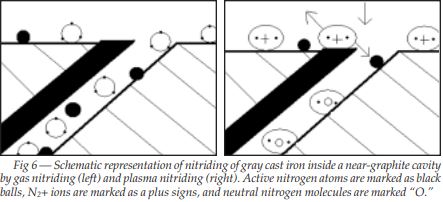
This was written by Edward Rolinski (sr. scientist, retired), and Gary Sharp (founder & CEO) at Advanced Heat Treat Corp. If you have any questions regarding heat treatments, please feel free to contact them at 319-232-5221.
- cast iron
- edward rolinski
- gas nitriding
- nitriding
- nitrocarburizing
- plasma nitriding
- stamping dies