posted
On Tuesday, December 8, 2020
in
Blog
Stamping Dies are Subjected to Severe Wear so Heat Treatment is Needed
Metallurgists are developing new steels to assist automotive engineers in designing better trucks, cars and SUVs [1]. Those steels are known as “3rd generation” Advanced High Strength Steels (AHSS) and Ultra High Strength Steels (UHSS) with tensile strengths of >1,000 MPa and good formability. Also, stamping of “mild steel” large components is still significant. Some of these materials (AHSS) can be cold-formed and the others (UHSS) have to be formed using hot stamping [1]. Substantial efforts and research have occurred in order to optimize the metal working operations needed to have flawless plastic deformation of those steels [2 and 3].
At the same time, when requirements for good, well-performing metal working tools - especially when stamping die demands grow significantly - heat treating companies make dramatic efforts to help improve the durability of those tools through thermochemical surface engineering [4-10]. Tools for stamping larger body panels such as roofs and body sides are typically made of cast irons and cast steels because they are economical and easy to fabricate. These stamping dies are subjected to severe wear and therefore have to be surface treated to improve performance, durability and the lifetime of the die.
Plasma ion nitriding offers the best tribological performance of the large-size cast stamping dies [5-10].
Plasma Ion Nitriding of Large Stamping Dies
Plasma treatment is carried out in a vacuum where the chamber wall serves as the anode and the load/dies have the cathodic polarization [8]. The process can be observed and monitored through optical methods since the glow discharge occurring near the cathode is very well visible through the port holes. Large stamping dies during plasma/ion nitriding are shown in Fig.1.
The main advantage of the process is its ability to form hard and uniform nitrided layers in alloyed or not-alloyed ductile and large gray cast iron stamping dies. Metallurgical details of such a layer are shown in Fig. 2. The layer is uniform and the process does not significantly affect surface roughness of the tool as the other alternative treatments may do [10].
Plasma-treated stamping dies undergo post-nitriding polishing and are ready to be used, see Fig. 3 a, b.
Fig. 3a: Stamping Die After Nitriding
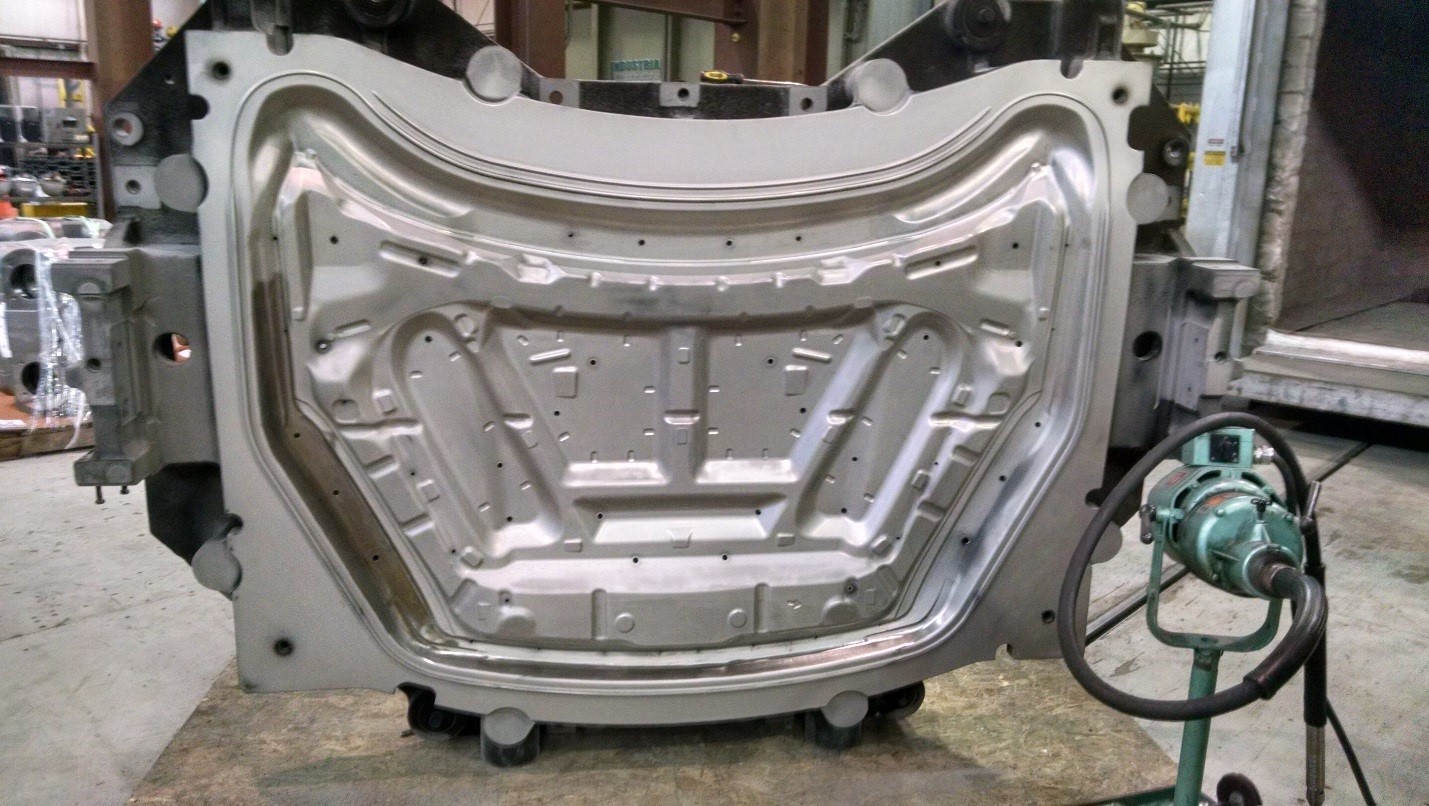
|
Fig. 3b: Die After Nitriding & Polishing
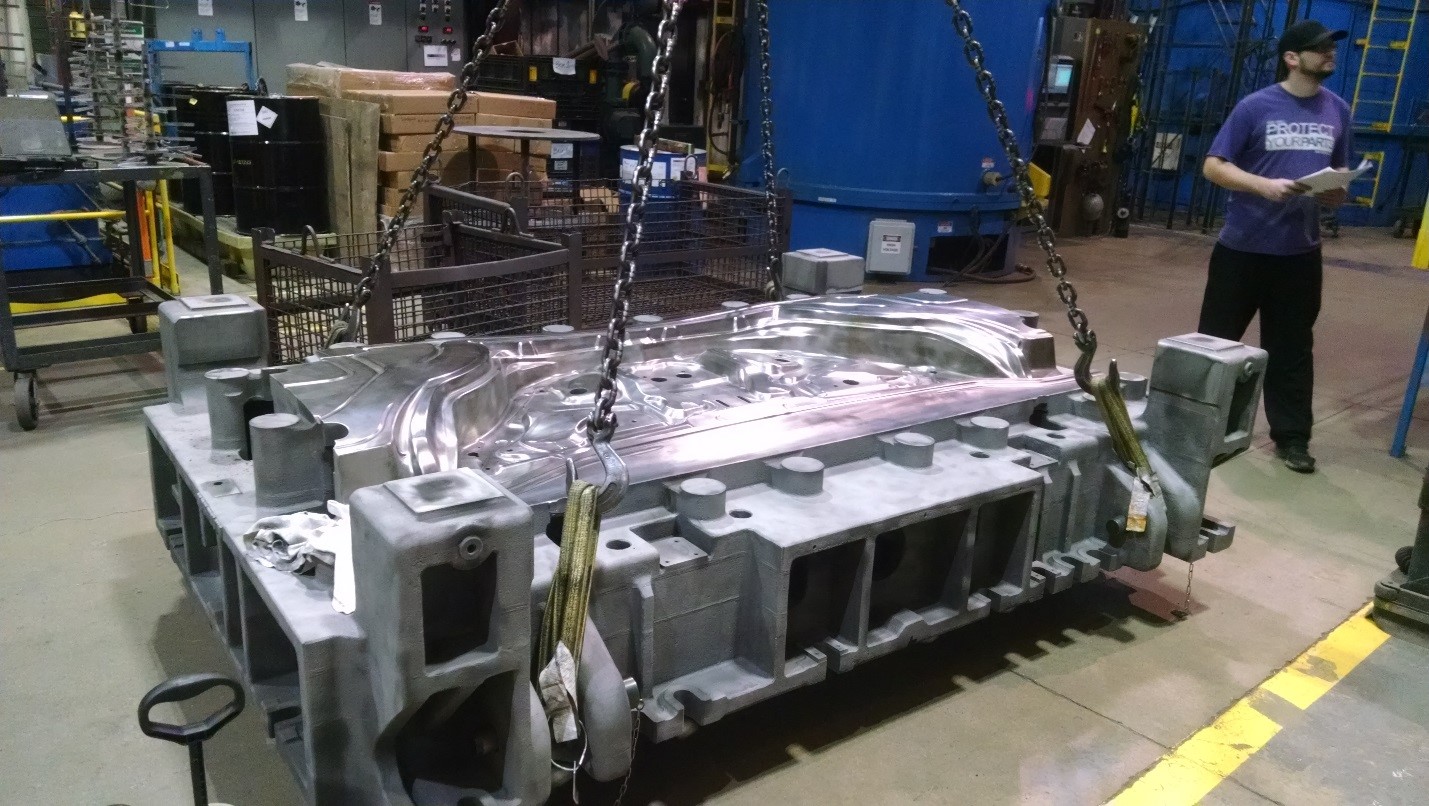
|
It should be noted that the plasma/ion nitriding process is carried out in the environmentally-friendly atmosphere of nitrogen with little hydrogen added, and the flow rate of these gases does not exceed 250 L/hr (about 9 cfh). Control of the layer structure and its hardness is very effective since plasma nitriding is a low-nitriding potential process allowing for producing defect-free nitrided layers without problems of cracking and exfoliations from the treated surface [8].
Do you have questions about improving the durability and life of your stamping dies? Contact us!
FILL OUT CONTACT FORM
This article was written for Industrial Heating by Advanced Heat Treat Corp.'s Dr. Edward Rolinski and appeared in the November 2020 issue. The magazine cover photo was courtesy of AHT in Cullman, Alabama.
SEE FULL MAGAZINE
References
1. G. S. Vasilash, “New Steels Explained: What You Need to Know about the Ongoing Developments”, AD&P, AUTOMOTIVE DESIGN & PRODUCTION, April 2020, Vol. 132 No.2, pp.30-34.
2. S. Golovashchenko and S. Nasheralahkami, “Determining sheared-edge formability of AHSS”, Stamping Journal, March/April, 2020, pp. 20-24.
3. A. Hedric, “Preventing stamping Armageddon”, Stamping Journal, March/April, 2020, pp. 18-19.
4. E. Rolinski and M. Woods, Engineering the Surface, Industrial Heating, March 2019, pp. 28-30.
5. E. Rolinski, J. Machcinski, J, McCann and M. Woods, “Silicon Enhancement of the Compound Layer for Tribological Application of Nitrided Hot-Work Steel”, Thermal Processing in Motion 2018—Conference Proceedings of the Thermal Processing in Motion, June 5-7, 2018, Spartanburg, South Carolina, USA, pp.129-136.
6. J. Senatorski, J. Tacikowski, E. Rolinski and S. Lampman, “Tribology of Nitrided and Nitrocarburized Steels”, ASM Handbook Vol 18,” Friction, Lubrication and Wear Technology”, ed. G. Totten ASM International, 2017, pp.638-652.
7. E. Rolinski, M. Woods, T. Damirgi, and G. Sharp, “Improving Performance of Stamping Dies with Ion/Plasma Nitriding” and “Ion Nitriding for Surface Hardening of Aerospace Components”, Industrial Heating, November, 2015, pp. 40-46.
8. E. Rolinski,” Plasma Assisted Nitriding and Nitrocarburizing of Steel and other Ferrous Alloys”, Chapter 11 in “Thermochemical Surface Engineering of Steels”, Ed. E. J. Mittemeijer and M. A. J. Somers, Pub. Woodhead Publishing, 2014, pp 413-449.
9. K. Agarwal, R. Shivpuri, J. Vincent, E. Rolinski and G. Sharp, “DC pulsed plasma deposition of nanocomposite coatings for improved tribology of gray cast iron stamping dies”, Journal of Materials Processing Technology 213 (2013), pp 864-876.
10. E. Rolinski, G. Sharp and A. Konieczny, “Plasma Nitriding Automotive Stamping Dies”, Heat Treating Progress, September/October 2006, Vol. 6, No 5, pp 19-23.
- automotive
- cast iron
- edward rolinski
- ion nitriding
- nitriding
- plasma nitriding
- stamping dies
- wear resistance