posted
On Tuesday, August 10, 2021
in
Blog
This paper was presented at PowderMet 2021. Click here to view the original PDF.
ABSTRACT
Surface hardening of the powder metallurgy (PM) products using nitriding methods can be realized with special precautions, taking the porous nature of the material under consideration. Typical response during gas nitriding of PM material when its density is below 7.5 g/cm3 is through-hardening of entire product with catastrophic embrittlement. This is a result of the ability of ammonia species to penetrate throughout the interconnected porosities, causing internal nitriding. Also, salt bath nitriding has unwanted effect of trapping the salt residue into the porosities.
On the contrary, plasma nitriding methods can be controlled more easily to avoid unwanted side effects related to excessively deep penetration of the material since majority of the active species are N2+ ions with a short mean path. However, there are also some ammonia species generated in plasma and they can go deeply into the structure of the material, similar to what is seen in the gas nitriding method. Therefore, proper control of plasma nitriding method should be utilized here for achieving a desired layer thickness and its proper structure. Plasma nitriding in a mixture of nitrogen and argon eliminates completely the formation of ammonia-type species and the layer that is formed has a thickness based only on plasma density, temperature, and time of the process.
INTRODUCTION
PM is a proven technology for manufacturing metal components. It is a near-net-shape technology with very little waste and few operations. These characteristics allows PM to be a low-cost solution for a variety of engineering applications [1-6]. Compared to wrought steels, heat treating of PM steels is more complex and significantly more parameters have to be considered when defining furnaces parameters and atmospheres [1-3]. There are considerable disagreements in the literature about the effect of the porosity on heat treatment [2-3]. Like wrought products, PM components benefit from secondary processing such as thermochemical treatment. Specifically, gas- and plasma-nitriding operations can be performed as a final operation to improve material characteristics of PM parts [7-21]. Some complications can be observed when thermo-chemical treatment is applied to sintered steels since the open-interconnected porosities cause problems when carburizing/nitriding and gas quenching agents penetrate deeply into the core of the product. In regards to thermochemical methods, plasma nitriding, as well a classical gas- and salt bath nitriding, with proper modification can be successfully used [8-11].
Nitriding offers low distortion, and nitrided parts are routinely shipped to final assembly after nitriding operations. This fact allows nitriding to further contribute to the inherently simple value chain associated with PM technology. Nitrided PM components have significantly increased surface properties such as wear resistance, bending fatigue and corrosion resistance [7, 12-16].
NITRIDING PROCESSES
Gas nitriding of PM material with 6.4 and 7.1 g/cm3 densities and open porosities carried out by J. Wendland [7] resulted in through-hardening of 10 mm-thick samples. In the same type of test, a similar sample with 7.5 g/cm3 density was nitrided as a regular, full-density material. Nitriding increased tribological properties of the high- as well as low-density PM. However, fracture toughness and bending fatigue properties of the low-density (<7.5 g/cm3) nitrided materials have to be considered as substandard. Problems with gas nitriding of the low-density PM were addressed by H. Ferguson who proposed steam sealing of the surface before hardening to limit penetration depth by ammonia [8].
Salt bath nitriding (also called liquid bath nitriding) is a method for surface hardening of similar materials as gas methods, but also with the same limitation; low-density materials will form a hard layer deeply below the surface, which will very likely have a negative effect on the fracture toughness and bending fatigue properties of the component. However, another problem with liquid bath nitriding of PM materials is potential for salt residue to be trapped in the inherent porosities. This contaminant, when left in the material, may be relieved during the regular work of a machine and can caused unwanted side effects such a corrosion and other issues. Modern versions of salt bath nitriding process often use a non-polluting bath with alkali metal cyanates and is carried out at 540-575° C [9].
Plasma/ion nitriding has been a very effective way of surface hardening of many machinery components made of PM in the automotive, agricultural, and other industries [11, 17-21]. Very broad possibilities to control the process allows avoiding the negative effects of the other nitriding methods [22, 28]. This will be shown in experimental data.
EXPERIMENTAL
FC-0205 powdered steel (per MPIF Standard 35) has been formed by admixing of elemental copper powder to elemental iron powder, and then was used to mold and sinter PM specimen with density 6.7g/cc for further experimental evaluation of various Nitriding processes. The samples with thickness of 8 mm were used in all processes. All experiments were carried out at temperature of 570° C (1058° F). Ferritic Nitrocarburizing (FNC) was performed with gas and salt bath processes. There were two gas-based processes; one regular FNC process and the other one steam sealing/pre-oxidizing with regular FNC. Plasma processing involved nitriding in atmospheres of nitrogen with hydrogen and addition of methane at two different pressures and atmosphere of nitrogen with argon.
Processes of ferritic nitrocarburizing involves diffusional addition of both nitrogen and carbon to ferrous surface at temperatures within the ferritic phase. The compound zone formed during these processes was predominately Ɛ-Fe2-3NC epsilon carbonitride+ ɣ’ (Fe4N) nitride with the exception of plasma process carried out in the mixture of nitrogen and argon where ɣ’ (Fe4N) nitride was present.
The samples were tested metallographically to detect and compare nitrided layers in the near surface areas. The microphotographs of all the samples are shown in Fig.1-6.
CONCLUSIONS AND DISCUSSION
It should be noted that both regular gas and salt bath FNC processes produced a layer with a very deep penetration into surface of the samples, Fig. 1 and 3. Even the sample treated initially by the steam sealing process had a “root-type” layer penetrating deeply into the surface grain boundaries although thickness of the outer layer was very moderate, Fig. 2. Evidently ammonia penetration into the surface was very deep. It should be also noted that the oxides formed during the steam sealing were still present in the structure and their role of reducing chemisorption of ammonia at the surface and stopping/minimizing nitriding below the surface was effective.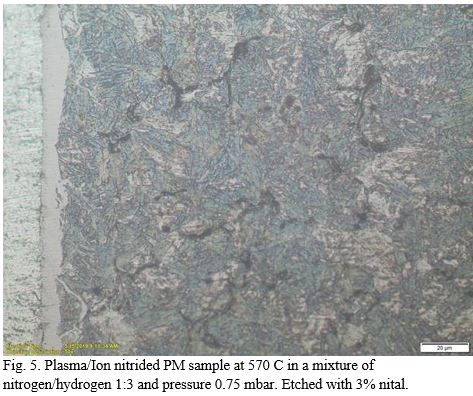
Salt bath treated sample appeared to be very aggressively nitrided and the “roots” of the layer were similar to the prior sample from the gas process, Fig. 3. This process known for its aggressiveness produced very likely a high nitrogen containing nitrides and carbonitrides [9].
Ion/plasma nitrided samples had a very well defined compound zone at the surface and deeper penetrating “roots” only when the processing gas pressure was high, Fig. 4. No deeper penetration of nitrides into the surface was observed when processing was at low pressure or without hydrogen. It should be noted here that major nitriding species in plasma process are N2+, N+ and NHx+ ions as well as the NH3 molecules and radicals formed near the cathode glow discharge [23-27]. When processing pressure is low, the number of the active ammonia-type species is reduced and there is no deep penetration of the interconnected porosities by the ions since their mean free path and life time is much shorter than ammonia [28], Fig. 5. Absence of hydrogen in the plasma eliminates ammonia-type species and there is no deep penetration of the layer into the open/interconnected porosities, Fig. 6.
Observations made during these experiments allow us to form following practical conclusion:
1. Ion/plasma nitriding and nitrocarburizing allows for a very precise control of the nitrided layer structure regardless of the presence of open/interconnected porosities in PM, low-density materials. Process can be carried out safely to produce a layer which would increase tribological as well as bending fatigue properties of the component without endangering fracture toughness of it. Corrosion resistance will also be increased after such treatment.
2. Gas and salt bath nitriding of PM components will increase significantly their tribological and corrosion resistance. However, bending fatigue properties and fracture toughness of the components will be very likely significantly reduced because of the extreme penetration. Exception might be only when the gas FNC/nitriding process is combined with the first step-steam sealing pre-oxidizing.
Questions about Nitriding Ferrous Powder Metal Products?
CONTACT US
REFERENCES
1. GKN SINTER METALS, THINK, Innovations in Powder Metal, https://www.gknpm.com/globalassets/downloads/powder-metallurgy/2018/gkn-overview-brochure-english.pdf,
2. B. Leupold, V. Janzen, G. Kotthoff and D. Eichholz, “Validation Approach of PM Gears for e-Drive Applications”, Power Transmission Engineering, Oct. 2019, pp. 49-55.
3. H. Ferguson, “The Heat Treatment of P/M Steels-an Overview”, Heat Treating Proc. of the 16th Conference, ASM, 1996, pp. 319-322.
4. H. Ferguson, “Heat Treatment of Ferrous Powder Metallurgy Parts”, ASM Handbook, Volume 7, ASM, Materials Park OH, USA, 1998, pp. 645-655.
5. H. Danninger, R. de Oro Calderon and C. Gierl-Mayer, “Alloy Systems for heat Treated Sintered Steels”, HTM J. Heat Treatm. Mat. 74 (2019) 5, pp. 282-292.
6. H. Danninger and M. Dlapka, “Heat Treatment of Sintered Steels-what is different?” HTM J. Heat Treatm. Mat. 73, 2018, pp. 117-130.
7. J. Wendland, “Shaping of user properties of sintered metal materials by controlled gas nitriding”, PhD Thesis, Politechnika Poznanska, Poznan, Poland, in Polish.
8. H. Ferguson, “Steam Sealing for Nitrogen Treated Ferrous Part”, US Patent no 4,738,730, Apr. 19, 1988.
9. D.Pye, Practical Nitriding and Ferritic Nitrocarburizing, 2003, Ed. ASM, pp. 201-218.
10. U. Huchel, S. Strämke, “Pulsplasmanitrieren von Sinterwerkstoffen”, Proc. 23 Hagener Symposium Pulvermetallurgie mit Fachausstellung, Hagen, Germany, 2004.
11. E. Rolinski, G. Sharp, K. Brondum and N. Peterson, “P/M Turbo Charger and Armature Components: Plasma Nitriding and Nitrocarburizing to Reduce Friction Wear”, 2005 SAE World Congress Detroit, Michigan, April 11-14, 2005, Paper 2005-01-0722, Ed. SAE International, Warrendale, PA 15096-0001-USA.
12. J. Čerňan, D. Rodziňák, M. Komolík, P. Hvizdoš, K. Semrád, “TRIBOLOGICAL PROPERTIES OF SINTERED STEEL FOLLOWING PLASMA NITRIDING”, Powder Metallurgy Progress, Vol.12 (2012), No 1 34.
13. L. Alzati, U. Engström, B. Rivolta, and A. Tavasci, “Wear Resistance of Gas Nitrided Astaloy CrLTM Sintered Steel”, PM2008 World Congress, Washington, USA, 2008.
14. Cristina IONICI, “FATIGUE BEHAVIOR OF SINTERED METAL PARTS FROM POWDERS”, Fiabilitate si Durabilitate - Fiability & Durability No 2/ 2016 Editura “Academica Brâncuşi”, Târgu Jiu, ISSN 1844 – 640X, pp. 170-173.
15. P. C. Borges, A. E. Martinelli and C. V. Franco, “Microstructure and corrosion behaviour of plasma-nitrocarburized sintered steel”, Materials and Corrosion, 2004, 55, No. 8, pp.594-601.
16. J. Wendland, J. Borowski, L. Małdzinski, “The influence of gas nitriding process on the structure and hardness of sintered metal Fe-based materials”, 2011, Obrobka Plastyczna Metali, Vol. XXII No2, pp. 75-82, in Polish.
17. E. Rolinski,” Plasma Assisted Nitriding and Nitrocarburizing of Steel and other Ferrous Alloys”, Thermochemical Surface Engineering of Steels, Ed. E. J. Mittemeijer and M. A. J. Somers, Pub. Woodhead Publishing, 2014, pp 413-449.
18. E. Rolinski, G. Sharp, “When and Why Ion Nitriding/Nitrocarburizing Makes Good Sense”, Industrial Heating, Aug. 2005, pp 67-72.
19. E. Rolinski, G. Sharp, “Ion Nitriding and Nitrocarburizing of Sintered PM Parts”, Industrial Heating, Oct. 2004, pp 33-35.
20. R. Gligorijevic, J. Jevtic, D. Borak, “Plasma Nitriding of Powder Valve Seat Inserts for Diesel Engines”, BALKANTRIB’O5 5th INTERNATIONAL CONFERENCE ON TRIBOLOGY”, 2005, Kragujevac, Serbia and Montenegro, pp. 352-355.
21. T. Bendo,1 H. C. Pavanati,2 A. N. Klein,1 A. E. Martinelli,3 and A. M. Maliska, “Plasma Nitriding of Surface Mo-Enriched Sintered Iron”, ISRN Materials Science Volume 2011, Article ID 121464, 8 pages.
22. E. Rolinski, G. Sharp, “Controlling Plasma Nitriding”, Materials Performance and Characterization, Vol. 6, No 4, 2017, pp.698-716, https://doi.org/10.1520/ MPC20160051. ISSN 2370-1365.
23. M. Hudis, ‘Study of ion-nitriding’, Journal of Applied Physics, 1973, 44, 1489-1496.
24. G.G. Tibbetts, ‘Role of nitrogen atoms in “ion-nitriding”, Journal of Applied Physics, 1974, 35, 5072-5073.
25. J. Walkowicz, "Comparative evaluation of the intensity of ion and gas nitriding processes on the basis of conformity analysis of nitrided layers phase composition with the Lehrer’s phase balance diagram”, Problemy Eksploatacji, 2003, 48, 1, pp. 45-53.
26. J. Walkowicz, P. Supiot, J. Smolik & M. Grushin, “The influence of the N2-H2 mixture composition on the spectroscopic and temporal behavior of glow discharge characteristics in pulse-supplied nitriding processes”, Surface and Coatings Technology, 2004, 180-181, pp. 407-412.
27. M., G. Skalecki, H. Klümper-Westkamp, F. Hoffmann, H. W. Zoch, S. Bischoff, J. Rohde, “Plasma nitriding potential and a new modeling approach for plasma nitriding process control”, Proceedings of the 28th ASM Heat Treating Society Conference, October 20–22, 2015, Detroit, Michigan, USA, pp 325-328.
28. E. Rolinski and M. Woods, “Plasma Nitriding Mechanisms of Low-Density Sintered Metal Products” / “Mechanismen des Plasmanitrierens von gesinterten Metallprodukten mit niedriger Dichte”, HTM J. Heat Treatm. Mat. 76, 2021, pp 58-63.
- edward rolinski
- ion nitriding
- nitriding
- plasma nitriding
- powder metal